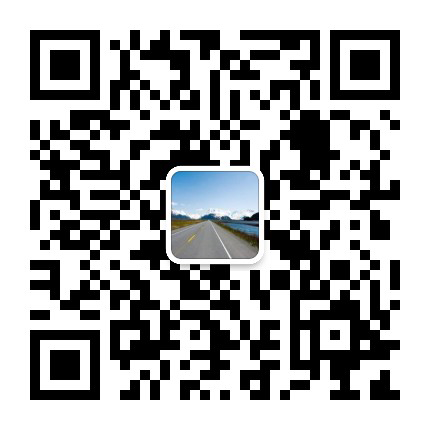
结合压铸件缺陷检测的现状和趋势,探讨在线和离线检测相结合的铝压铸件质量控制技术,并基于安顺工业CT测量机对铝压铸产品进行离线高精度扫描测量分析。,并结合流水线边缘或在线高速CT检查方法,结合该方法可以有效地阻止整个生产过程中的质量保证和质量异常,并快速跟踪缺陷信息,从而显着提高压铸质量。这种方法可以在最短的时间内识别,清除和隔离异常压铸件,从而达到良好的质量控制和提高企业市场竞争力的目的。
目前,国内的铸件生产车间大多采用破坏性检查和人工目视检查的方法,劳动强度大,效率低,检查结果容易受到操作者主观影响。
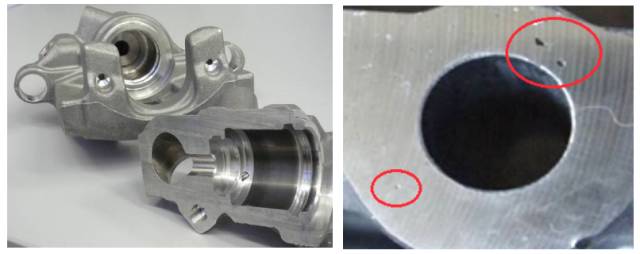
图1: 传统破坏性检验及目视检测法
一些压铸制造商使用常规的X射线摄影技术来检测铝压铸件,铝压铸件具有检测速度快和操作简单的特点,但通常仅提供二维平面投影信息。在射线照相方向上,缺陷之前和之后的图像重叠,这是较高的。对于缺陷的深度,厚度和三维信息,不能直接或准确地给出错误判断缺陷的可能性。但是,确定缺陷的大小和位置的重要性与确定产品安全性能密不可分。准确的定量分析和三维尺寸测量在汽车等行业的制造链中越来越受到重视和应用。
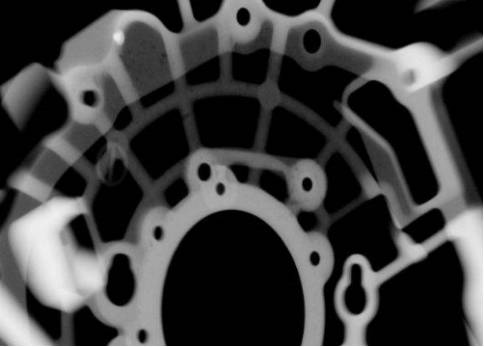
图2: 工业X 光机检测二维平面图像
迁移趋势:高精度3D CT扫描检查
工业CT是工业计算机断层扫描成像技术的缩写。以锥形束CT为例,其基本原理是锥形束穿过被测物体并衰减。通过平板检测器可以获得大量没有图像重叠的断层图像。根据重构算法,重构完整的三维图像。作为当今最好的无损检测方法之一,它可以获取更全面的产品内部和外部质量数据,并更有效地反映缺陷的视觉图像的内部结构,形状,大小和分布,并且在铝压铸缺陷检测领域中越来越广泛地使用。
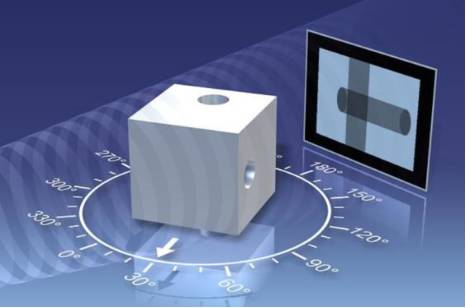
图3: 锥束计算机断层扫描成像
作为主要应用之一,工业CT可以实现三维缺陷和二维缺陷的自动测量,分析和显示。所检测到的缺陷的大小可以通过颜色编码直观地显示,并且可以获得每个缺陷的各种参数(缺陷位置,大小)。以及几何形状(体积,坐标,投影区域),最近的缺陷间隔,每个缺陷到参考表面的距离,总体百分比或孔隙率的统计信息以及缺陷体积直方图,可以根据标准(例如P201)来定位切片图像和VW 50097孔隙率分析。这种方法消除了费时的样品制备和显微照相。可以将分析过程另存为模板,以实现对所有样品的快速重复分析并减少人工干预。
随着工业CT的发展规模日益多样化,具有测量性能和可追溯性测量精度的工业CT测量机在综合性能方面,尤其是在铝铸坯的尺寸和形状公差方面,具有更强的可扩展性。-模拟比较/实际值比较,反向工程和其他需要精确测量应用程序的领域。
大型铝压铸件的CT扫描
以数模比较/实际值比较为例,CT 3D体素数据可以直接与CAD或其他CT 3D体素数据进行比较,比传统方法效率更高,并且可以通过颜色标记显示分析结果。分析整个对象或用户指定的“感兴趣区域”,并且可以直接在CT 3D体素数据上执行数模比较,而无需将3D数据间接转换为点云或STL数据,从而避免了间接测量的增加不确定性和有效信息的丢失。
大趋势:离线,在线或在线检测的集成
近年来,随着产品技术的飞速发展和日益激烈的市场竞争,为了确保产品质量和经济效益,先进,优化的控制技术被广泛应用于压铸工艺中。但是,无论是在先进控制策略的应用过程中,还是在直接控制产品质量的过程中,最困难的问题之一就是难以在线实时测量压铸产品的质量变量。过去,受制程和技术的限制,一些重要的制程参数和产品内部质量指标很难或不可能通过硬件传感器在线检测。最近,随着国外知名公司实施先进的高速CT系统解决方案,这一问题将得到有效解决。
应用于宝马集团的德国铝压铸厂
通常,在生产过程中需要对每台机器进行检查,对生产的产品进行离线分析和采样,然后发送到测量实验室进行手动分析,以确认产品的即时一致性,并指导产品的生产过程。基于分析价值的生产。由于时间滞后,远不能满足在线过程控制的要求,并且不可避免地会增加生产现场的生产线或在线高速CT的边缘。它逐渐被开发以解决对质量变量的实时测量和控制。在线测试为过程控制,质量控制,过程管理和决策提供支持,并为进一步实现质量控制和过程优化奠定基础。